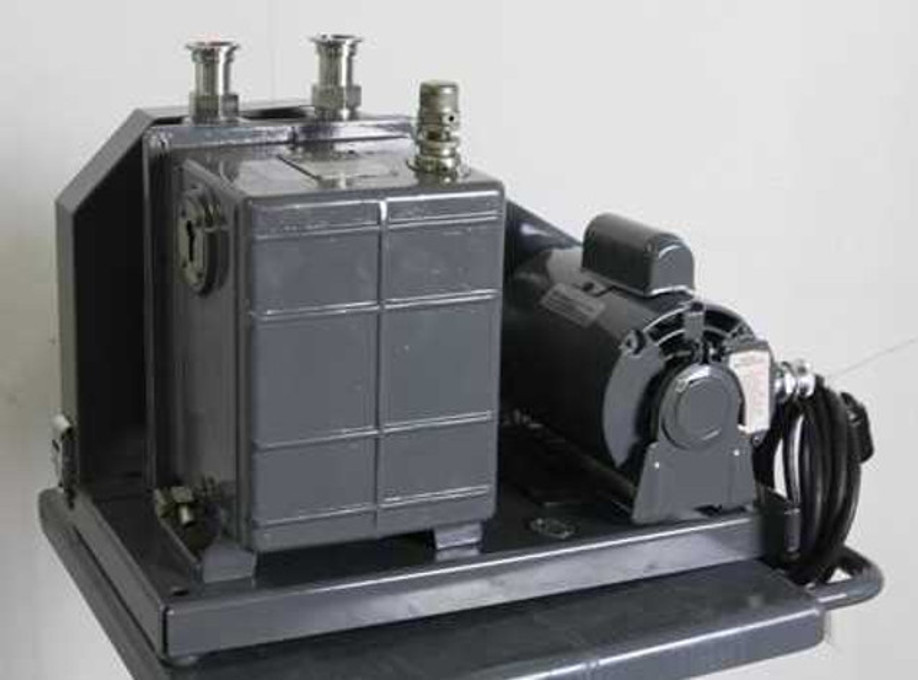
The Benefits of Teflon or Non-Corrosive Seals on Rotary Vane Oil Vacuum Pumps: Enhancing Performance and Longevity
Posted by Michael Hnatow on 22nd Jun 2023
Introduction:
HiTechTrader has always had some oil vacuum pimp in stock. Rotary vane oil vacuum pumps are widely used in various industries for their efficiency and reliability in creating and maintaining vacuum environments. The selection of appropriate seals for these pumps is crucial for ensuring optimal performance and durability. In this technical memo, we will explore the benefits of using Teflon or non-corrosive seals in rotary vane oil vacuum pumps and their positive impact on performance and longevity.
Chemical Resistance:
Product Wlech 1402N Chemstar
Teflon and non-corrosive seals offer excellent chemical resistance, making them highly suitable for applications involving aggressive chemicals or corrosive gases. These seals can withstand exposure to a wide range of chemicals, including acids, bases, solvents, and reactive gases, without deteriorating or compromising their sealing properties. By utilizing Teflon or non-corrosive seals, the risk of seal degradation, leakage, and pump failure due to chemical exposure is significantly minimized, ensuring long-lasting and reliable pump operation.
Enhanced Lubrication:
The use of Teflon or non-corrosive seals in rotary vane oil vacuum pumps can improve the lubrication process. Teflon seals, for instance, have low friction coefficients and exhibit self-lubricating properties, reducing friction and wear between the vanes and the pump housing. This results in smoother operation, reduced heat generation, and extended vane and bearing life. Non-corrosive seals, on the other hand, maintain the lubricating properties of the oil by preventing contamination or chemical reactions that could degrade the oil's performance. Improved lubrication translates to enhanced pump efficiency, reduced maintenance requirements, and cost savings in the long run.
High-Temperature Stability:
Product: Edwards RV12
Teflon and non-corrosive seals exhibit excellent thermal stability, making them suitable for high-temperature applications. These seals can withstand elevated temperatures without losing their sealing integrity or deforming, ensuring consistent and reliable performance even under demanding operating conditions. The ability to handle high temperatures effectively expands the range of applications for rotary vane oil vacuum pumps, allowing them to be utilized in processes that involve heat, such as thermal distillation, drying, or high-temperature reactions.
Reduced Contamination:
Teflon and non-corrosive seals minimize the risk of contamination in vacuum processes. These seals have low particulate generation and are chemically inert, reducing the chances of introducing contaminants into the vacuum system. By using Teflon or non-corrosive seals, the purity and cleanliness of the vacuum environment can be maintained, which is crucial in sensitive applications such as semiconductor manufacturing, analytical instrumentation, and research laboratories.
Longer Service Life:
The combination of chemical resistance, enhanced lubrication, high-temperature stability, and reduced contamination offered by Teflon or non-corrosive seals contributes to extended service life for rotary vane oil vacuum pumps. By minimizing wear, reducing the risk of chemical attack, and maintaining efficient lubrication, these seals help preserve the pump's performance and reliability over an extended period. This results in reduced downtime, lower maintenance costs, and increased productivity.
Chnaging oil in a vaccum pump conclusion:
In summary, the utilization of Teflon or non-corrosive seals in rotary vane oil vacuum pumps provides numerous benefits, including chemical resistance, enhanced lubrication, high-temperature stability, reduced contamination, and extended service life. These seals offer superior sealing performance, ensuring reliable operation and protecting the pump from chemical degradation or failure. By adopting Teflon or non-corrosive seals, industries can optimize the performance and longevity of their rotary vane oil vacuum pumps, enhancing efficiency, reducing maintenance requirements, and maximizing productivity.